Newsroom
Analysis of processing shrinkage of large girth gear
2019-07-23 | Editor:
The large girth gear is generally cast steel material for processing and casting. Because the steel casting material has the characteristics of thermal expansion and contraction, it is processed during the process. It is necessary to control the shrinkage of the large girth gear castings, otherwise the size of the girth gear will change, which will affect the later processing.
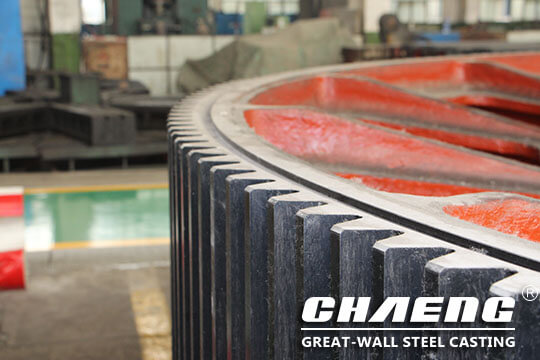
When a steel casting manufacturer produces a large girth gear and waits for its cooling, the size of the steel will shrink. This is what we call shrinkage. The amount of shrinkage usually needs to be expressed by the body shrinkage rate or the linear shrinkage rate. The metal changes from the liquid state to the normal temperature. The change in volume is the body shrinkage. The metal changes from high temperature to normal temperature in the solid state. A change in size is the line shrinkage. The shrinkage of the large girth gear is mainly divided into three stages: liquid shrinkage, solidification shrinkage, and solid shrinkage. The main reason for the shrinkage is the corresponding factors, as well as the chemical composition of the casting, as well as the temperature of the casting. The casting structure and the conditions of the mold are all related.
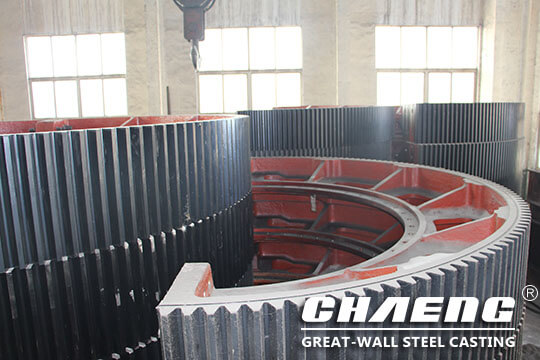
The shrinkage ratio of the large girth gear alloy elements of different compositions is also different. For example, if the carbon element contained in the carbon steel increases, the solidification shrinkage rate also increases, and the solid shrinkage rate decreases. If the content of carbon and silicon contained in the cast iron is higher, the sulfur content is lower, and the shrinkage rate is also smaller. The casting temperature has a control range of 50-150 degrees Celsius above the liquidus temperature, in order to reduce the shrinkage of the alloy liquid. If the wall thickness of the casting is not uniform enough, the cooling speed of each part will be different, and the shrinking sequence will be inconsistent. After mutual restraint, a certain resistance will be generated. If the large girth gear receives more mechanical resistance, the actual shrinkage rate will be smaller. Therefore, when making the model, the shrinkage rate needs to be considered, otherwise the casting material will be wasted, or the size will change. Mechanical mismatches directly reduce work efficiency.
Large casting foundries suggest that when casting a machining model for a customer, in addition to processing according to the requirements of the drawings, the shrinkage rate should also be considered, otherwise it will not be able to provide customers with complete products.
Order online
Fill out your message and submit it . Options with * must be filled in.
Prev:What is the production method for high quality slag pots?
Next:What is the impact on the service life of the slag pot?
PRODUCTS
CONTACT
- Tel: +8615290747879
- Whatsapp: +8615290747879
- E-mail: casting@chaeng.co
- Skype : GreatWall1958