Weight | >1 Ton |
Material | ZG45, ZG42CrMo |
Application | Ball Mill, Rotary Kiln,Rotary dryer |
Customizable | Yes |
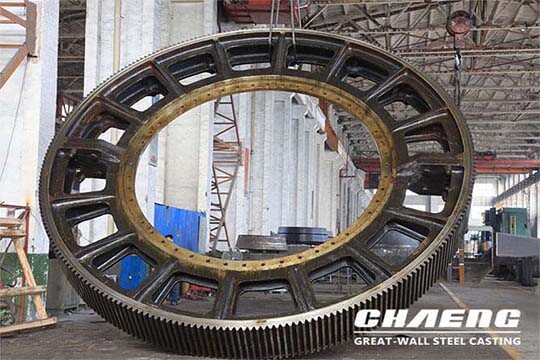
1. Special Heat Treatment Technology
Great Wall Steel Casting adopts special heat treatment technology to optimize structure, improve hardness and enhance impact resistance of girth gear.
2. Long Service Life
Great Wall Steel Casting adopts high strength steel to produce girth gear. Firstly characteristics optimization of rotary kiln is done to guarantee its stability during long time operation, also to prolong its working life.
3. Factory Price Custom & Quick Delivery
Great Wall Steel Casting has strong steel casting production capability, and it can provide girth gear in large quantity with short period.
Girth Gear (Rotary Kiln or Ball Mill) Quality Testing:
Girth gear rim is casted in two halves
Non destructive testing is performed to ensure zero defects
Machining of gear in multiple steps to ensure best finish and accuracy
Final quality inspection to ensure CPG quality
Specification
Specification |
|
Item |
Casting Steel Girth Gear |
Pressure angle |
Customized |
Material |
Alloy steel & Carbon steel |
Application |
rotary kiln, ball mill, rotary dryer,etc. |
Packing |
Seaworthy plywood packaged on stell pallets or as customers’ request |
Delivery date |
Depends on the amount and dimension of products |
Why quality is so important?
Total Girth Gear installation cost survey
Calculation example:
Kiln size ø5.0 x 90 m Production: 4500 tpd
• Estimated cost of parts: EUR 450.000,- (27%) Girth gear + springs etc.
• Est. mech. erection costs: EUR 130.000,- (8%) 29% of parts cost
• Estimated consequential loss : EUR 1.080.000,- (65%) EUR 4500/hour in 10 days
• Total installation costs: EUR 1.660.000,- (100%) Parts 27% Consequential 65% Mech. 8%
Conclusion:
• The cost of the Girth Gear is only a “piece of the cake” compared with the total substantial installation cost.
• Long term solution with Great Wall Casting quality is the best solution to ensure a beneficial investment.
How to Install the girth gear(rotary kiln):
The girth gear is placed near to a kiln tyre so that it is accurately aligned with the rotary kiln axis, with minimal wobble. It is normal for the nearby tyre to be fixed in position with thrust rollers, so that as the kiln expands on warming up, the turning girth gear position remains fairly constant, while the nose and tail of the kiln expand outward.
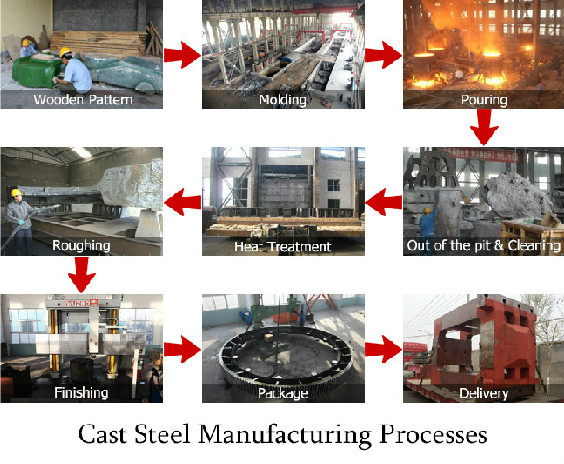
Great Wall Steel Casting’s big gears are applied in rotary kiln and ball mill of 5000 tpd cement production line in domestic famous cement enterprises, such as Xinjiang Tianshan Building Material Group, Henan Mengdian Group, etc. and provide reliable guarantee to normal operation of rotary kiln and ball mill.
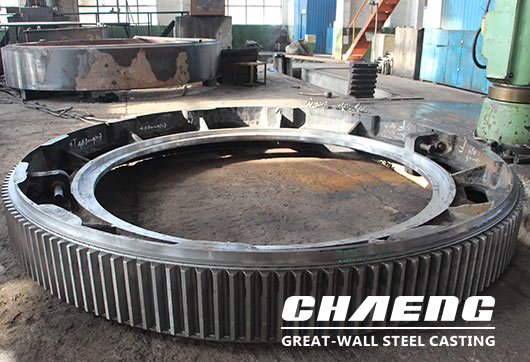
- Tel: +8619838076183
- Whatsapp: +8619838076183
- E-mail: casting@chaeng.co
- Skype : GreatWall1958