Weight | 1-80 Tons |
Material | ASTM: 1045 / DIN: CK45 |
Application | Rotary Kiln |
Customizable | Yes |
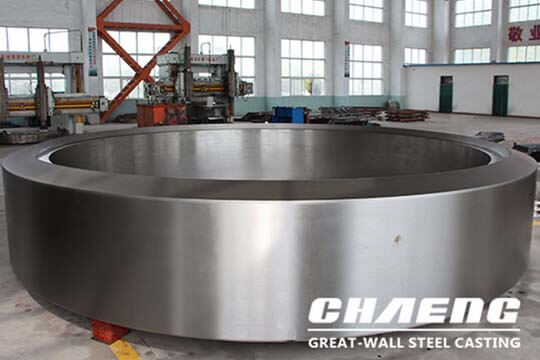
1. High strength and excellent durability.
CHAENG adopts quality materials ZG45 and ZG42CrMo to manufacture the kiln tyre to guarantee its strength and toughness, so as to support rotary kiln well.
2. The advanced process of double medium quenching enhances strong adaptability
After double medium quenching, each part of the rotary tyre is forged evenly. It has characters of high stiffiness on quenching, high toughness, and good wear resistance, suitable for various bad working environments.
3. CAE software digital simulation technology is used to assist in quality prediction and process optimization.
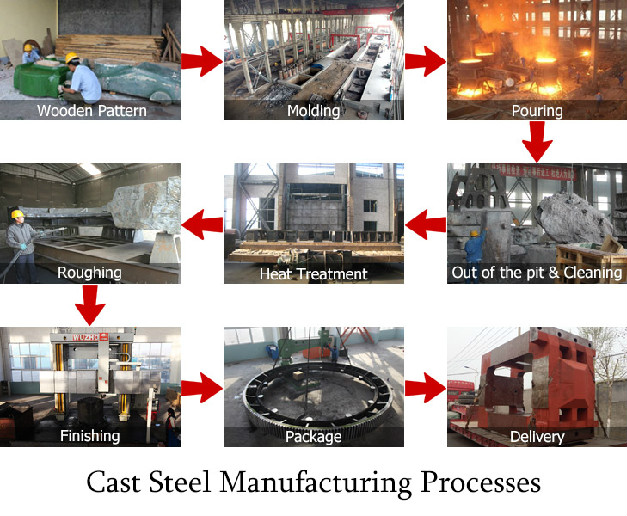
Kiln tyres manufactured by Great Wall Steel Casting have been exported to many countries abroad, including Italy, Turkey, and Chicago.
Note:
CHAENG (Great Wall Casting) can manufacture all types of rotary kiln tyre according to customers’ drawings and sizes. You are warmly welcomed to visit our company!
- Tel: +8619838076183
- Whatsapp: +8619838076183
- E-mail: casting@chaeng.co
- Skype : GreatWall1958