Newsroom
Key points of pouring process for 5.2m rotary kiln trunnion roller
2021-12-17 | Editor:
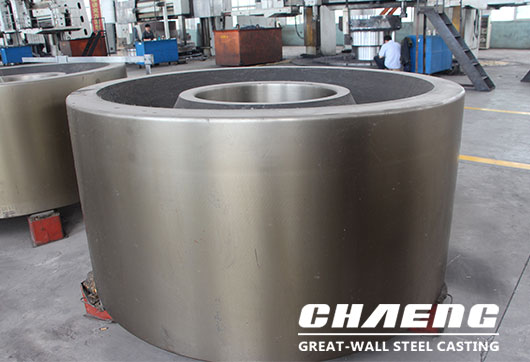
Pouring position:
The pouring position refers to the position of the casting in the mold during pouring. The correct pouring position should be easy to obtain qualified castings so that the entire casting process is as simple as possible and easy to control. To choose the pouring position correctly, the following basic principles should be followed:
1. The principle is that important surfaces and large planes are not upward. This is because various casting defects, such as pores, hole inspections, sand holes, and sand inclusions, are prone to appear on the top of the casting position.
2. The principle of the thick part upwards, try to place the thick part on the top, to achieve sequential solidification, easy to feed the riser. This is especially true for alloys with large shrinkage.
3. The principle that the thin-walled part is not upward to prevent insufficient pouring and cold isolation
4. The pouring position should also help reduce the number of sand cores, make the sand cores easy to fix, and easy to vent.
Control of casting temperature:
Pouring temperature is too high:
1. Conducive to the forming of castings
2. It is easy to cause defects such as shrinkage, shrinkage, surface sticky sand, swelling, etc.
3. High pouring temperature, slow cooling after pouring, castings are prone to surface pits, surface layer decarburization, and other defects
4. It may make the crystal grains of the castings coarse and cause the mechanical properties to decrease
Pouring temperature is too low: the casting is difficult to form, easy to produce cold barriers, insufficient pouring, shrinkage porosity inside the casting, and increased inclusions
Pouring speed control:
Too fast is conducive to the forming of the casting; it is easy to be involved in bubbles and inclusions; if the impact force is too large during pouring, the molten steel will splash and cold beans will be easily produced
Too slow is not conducive to the forming of castings, and castings are prone to defects such as cold isolation and insufficient pouring
It can be seen that the casting process has a vital influence on the quality of the rotary kiln trunnion roller, and it must not be taken lightly during the casting process of the rotary kiln trunnion roller. However, the usual method of Great Wall Cast Steel is to simulate the entire casting process with digital simulation technology before casting, so as to optimize the casting process and reduce the impact on the quality of the rotary kiln trunnion roller during the casting process.
It can be seen that the casting process has a vital influence on the quality of the rotary kiln trunnion roller, and it must not be taken lightly during the casting process of the rotary kiln trunnion roller. However, the usual method of CHAENG is to simulate the entire casting process with digital simulation technology so as to optimize the casting process and reduce the impact on the quality of the rotary kiln trunnion roller during the casting process.
Order online
Fill out your message and submit it . Options with * must be filled in.
PRODUCTS
CONTACT
- Tel: +8615290747879
- Whatsapp: +8615290747879
- E-mail: casting@chaeng.co
- Skype : GreatWall1958