Newsroom
Our Grinding Mill Manganese Wear Parts
2015-12-18 | Editor:
MnSteels supplies Manganese Wear Parts for Grinding Mill Grinding Rings and Grinding Roller.
MnSteels has the capacity to supply grinding mill wear parts within the following parameters:
Maximum weight: 3 t
Maximum diameter: 2500mms
Maximum wall thickness: 300mms
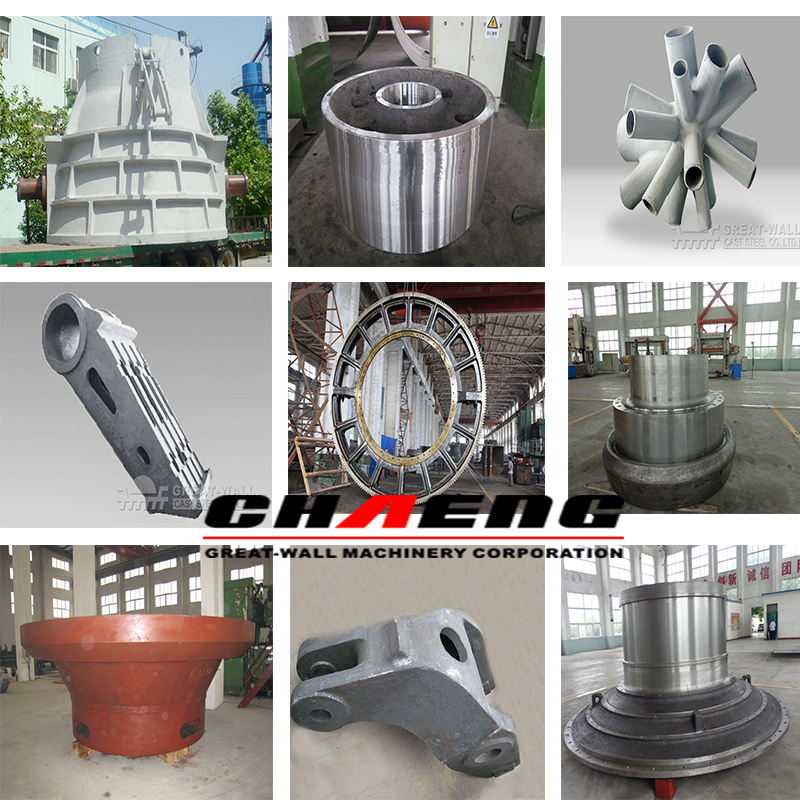
Production Tour:
MnSteels has always been trying to produce "proper" manganese steel castings; quality control and process management play a very important role in our day to day tasks.
Let’s take a tour on how we make our products:
1.Our sales team takes orders from our customers:
2.When a new product is introduced, our design team “translates” the drawings supplied into product sheets:
3.A 3D model of the product is generated for better understanding.
4.Technicians then performs simulations to determine best quality control method.
5.MnSteels uses STEEL patterns.
6.Products are poured using bottom pour ladle.
7.After 72 hours of cooling time, gating and risers (feeders) are ready to be removed.
8.MnSteels uses computer controlled heat treatment furnaces for all of our products.
9.MnSteels uses running water for quenching.
10.Products are grinded, getting ready to be machined.
11.Products are being carefully tooled so they can be installed properly.
12.Liners are painted as per customer’s requests.
13.MnSteels Crusher liners then being shipped to our customers all around the globe.
MnSteels has the capacity to supply grinding mill wear parts within the following parameters:
Maximum weight: 3 t
Maximum diameter: 2500mms
Maximum wall thickness: 300mms
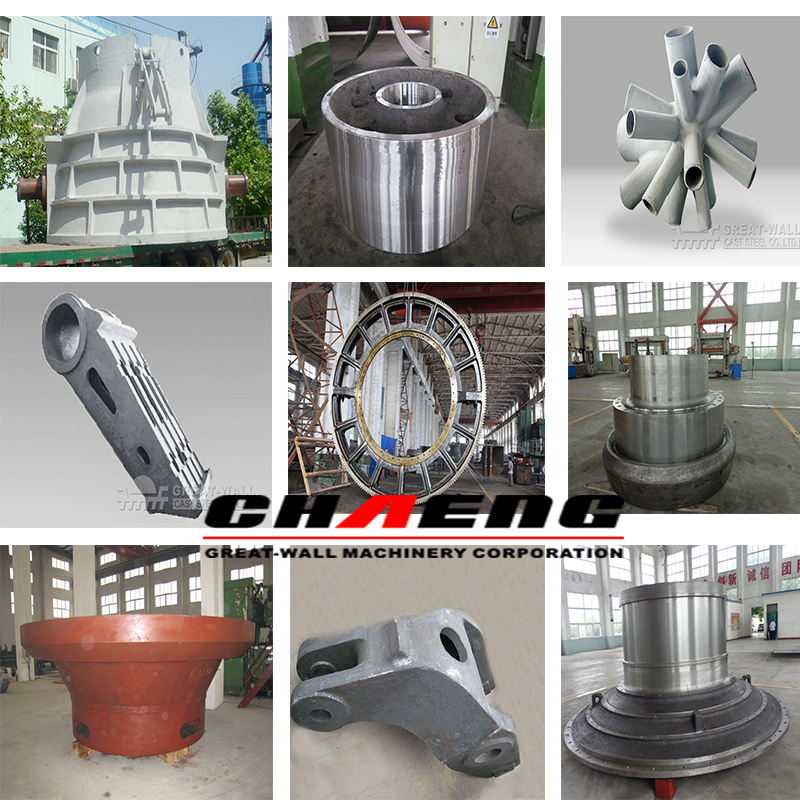
Production Tour:
MnSteels has always been trying to produce "proper" manganese steel castings; quality control and process management play a very important role in our day to day tasks.
Let’s take a tour on how we make our products:
1.Our sales team takes orders from our customers:
2.When a new product is introduced, our design team “translates” the drawings supplied into product sheets:
3.A 3D model of the product is generated for better understanding.
4.Technicians then performs simulations to determine best quality control method.
5.MnSteels uses STEEL patterns.
6.Products are poured using bottom pour ladle.
7.After 72 hours of cooling time, gating and risers (feeders) are ready to be removed.
8.MnSteels uses computer controlled heat treatment furnaces for all of our products.
9.MnSteels uses running water for quenching.
10.Products are grinded, getting ready to be machined.
11.Products are being carefully tooled so they can be installed properly.
12.Liners are painted as per customer’s requests.
13.MnSteels Crusher liners then being shipped to our customers all around the globe.
Order online
Fill out your message and submit it . Options with * must be filled in.
Prev:cement mill spare parts detailed installation methods
Next:Improve casting machinery technology to promote the development of casting industry
PRODUCTS
CONTACT
- Tel: +8619838076183
- Whatsapp: +8619838076183
- E-mail: casting@chaeng.co
- Skype : GreatWall1958