Newsroom
How to deal with cracks in the rotary kiln shell
2019-03-06 | Editor:
As a large steel casting production base in the north of Henan Province, CHAENG (Xinxiang Great Wall Steel Casting) can provide rotary kiln shells, rotary kiln support rollers, kiln tyre, vertical mill grinding roller & table, ball mill girth gears, etc. CHAENG has rich experience of cooperation with many cement manufacturing companies, today let’s talk about how the cement plant to prevent the cracks of rotary kiln shell.
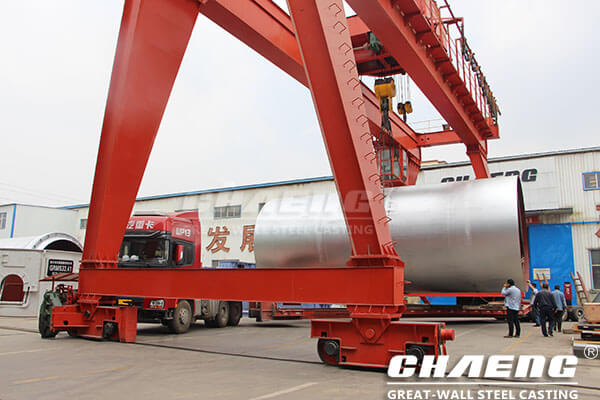
1. Preventive measures for longitudinal cracks
The main causes of longitudinal cracks in the rotary kiln shell are caused by insufficient rigidity of the shell, large temperature stress and additional stress. Therefore, in the design and manufacture process of the rotary kiln, the thickness of the cylinder shell should be appropriately increased. According to the relevant information, the thickness of the kiln shell under the tyre should not be less than 1.5% of the nominal diameter of the cylinder. The thickness of the stopper of the floating pad should not be greater than 50% of the thickness of the cylinder, and the width of the stopper should not be greater than 200mm, to reduce the additional stress and temperature stress caused by uneven deformation of the cylinder because of the support reaction force. The area of the pad should not be lower than 60% of the internal control surface area of the tyre, and the height of the weld of the stopper and the cylinder should be controlled at about 60% of the thickness of the stopper. And there shall be no defects such as undercuts to avoid local stress concentration and damage on cylinder.
In the installation process, not only the cold state accuracy should be considered, but also the hot state accuracy during operation. Predict the operating temperature of the tyre at each gear, calculate the amount of center rise in the hot state of each gear, and make installation adjustment, to make the force on the rotary kiln at each gear in the long-term operation is close to the design level, avoiding excessive cracking due to the increase of the center of a certain gear; in the production and maintenance, protect the kiln skin and the refractory brick, to prevent the cylinder from the large axial and axial temperature difference which will cause the cylinder to bend, and result in the additional stress because of limited expansion and contraction of local cylinder. When the rotary kiln is faulty, such as the watt heat, it must not be unloaded regardless of the cause, causing the cylinder to deviate from the center line. It is also impossible to cool the cylinder sharply when the red kiln or cylinder temperature is too high.
2. Preventive measures for circumferential cracks
In order to prevent the circumferential crack, the thickness of the cylinder should be fully considered in the design and manufacture. The thickness of the transition cylinder should be close to the average of the thickness of the lower cylinder and the thickness of the intermediate cylinder to facilitate the smooth deformation, and the stress is easy to spread and reduce the stress concentration. The key to prevent the crack at the weld between the cylinder and the spring plate of the large ring gear is to ensure that the rigidity of the cylinder is greater than the stiffness of the spring plate. The thickness of the cylinder under the large ring gear should not be lower than the 1% of the nominal diameter, the thickness of the spring plate should be about 60% of the thickness of the cylinder, which is beneficial to digest the external force through the deformation of the spring plate, to alleviate the damage of the external force to the weld; in the production and maintenance, we must also ensure the longitudinal temperature of the cylinder The circumferential temperature difference is less than 50 °C, which reduces the additional bending stress and temperature difference stress.
3. Prevention of cracks in the transition zone of rotary kiln
The main reason of cracks on the transition zone is that the cylinder is thinned by the corrosion of alkaline gas and alkaline materials in the kiln. Therefore, we must first consider the isolation of alkaline materials from the metal cylinder to reduce corrosion. There are several aspects of the measures. First, the high-temperature anti-corrosion coating can be painted on the inner surface of the cylinder; the second is to grout the wet refractory brick to eliminate the brick joint and isolate the alkaline material from the metal cylinder to prevent or relieve stress and chemical corrosion and prolong the life of the cylinder. It is also possible to extend the life of the cylinder by increasing the thickness of the cylinder (e.g., increasing the thickness of the cylinder to 0.7% of the nominal diameter of the cylinder).
4. Other preventive measures for cracks in the cylinder
Such as protecting the kiln skin, protecting the refractory brick, preventing the temperature of the cylinder from being uneven or too high, ensuring the mechanical properties of the cylinder material, ensuring the straightness of the cylinder under the operating condition, and reducing the additional load; the normal control of the speed of the kiln body up and down is strictly prohibited. Accelerate the top kiln; prevent the large and small gears from biting the roots, increase the radial top force, and so on. If there is crack in the kiln cylinder, the crack should be stopped in time and effectively welded to prevent the crack from extending. At the same time, the welding position should be selected at 45° on the horizontal centerline, because the lateral stress is zero here; The crack of the cylinder is detected. If the cylinder has been corroded and the corrosion amount has reached about 30%, it is necessary to replace the cylinder to prepare, otherwise it will cause a big accident.
It is recommended to check the centerline and the thickness of the rotary kiln, and reduce the additional load of the cylinder, to prolong the life of the rotary kiln.
If you need to replace you rotary kiln shell, contact CHAENG! CHAENG has strong casting and machining capabilities, and large annual output. We strictly follows the level-2 national inspection standard and implements 360° non-destructive testing system to ensure the quality of steel castings. CHAENG has close cooperation with many companies of various industries, supplying them with spare parts with good performance to improve the practical effect of the equipment and extend the service life of the equipment.
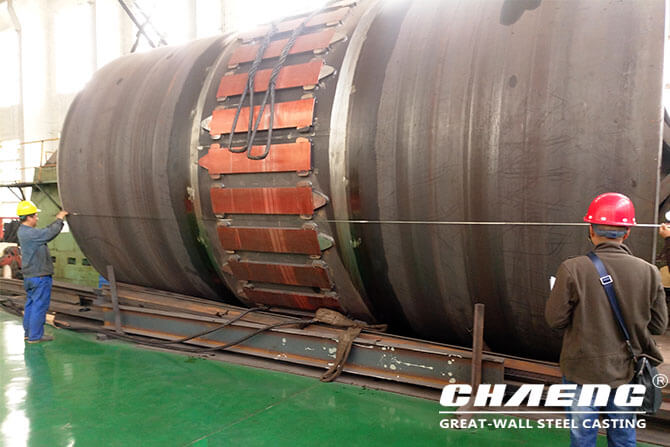
Order online
Fill out your message and submit it . Options with * must be filled in.
Prev:Why to buy rotary kiln riding ring from CHAENG
Next:Metal China 2019 - CHAENG invites you to the 17th China International Foundry Expo
PRODUCTS
CONTACT
- Tel: +8615290747879
- Whatsapp: +8615290747879
- E-mail: casting@chaeng.co
- Skype : GreatWall1958