Newsroom
Casting girth gear fabrication process
2017-12-28 | Editor:
CHAENG is experienced in manufacturing steel castings through sand casting process, and has advanced casting equipment and process technology, can supply high quality steel castings for customers. Especially the key product girth gears have been exported to many countries and areas to assist the operation of customers’ ball mill and rotary kiln.
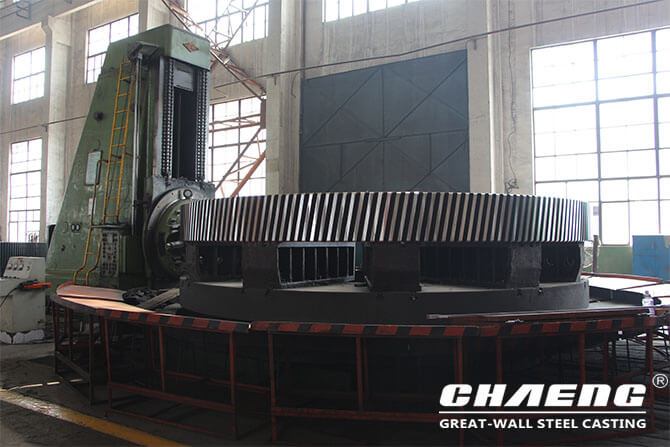
CHAENG adopts adopts the advanced water glass sand molding process, which has higher density and viscosity. And CHAENG has professional technical team to strictly control molding size and molten steel temperature, so as to strengthen hardness and wear resistance.
The making process of CHAENG casting girth gear:
Base on the requirements of customers, CHAENG selects appropriate wooden mold for modeling design, and uses CAE software to simulate the casting process. Strictly according to the process procedures to produce high-quality girth gear:
wood mold - modelling - pouring - heat preservation - out of the pit, sand cleaning - heat treatment - roughing, finishing - packing and delivery.
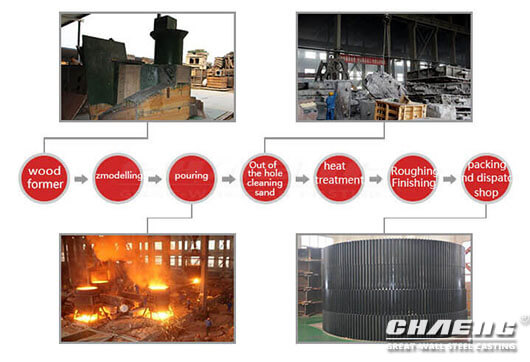
The first step: Simulation and modeling
Before casting, numerically simulate the casting process by CAE software to analyze the molding process, predict and optimize the product quality. Metallurgical auxiliary devices are complete to control the overall size well. Water glass sand molding process can prevent the hot cracks on castings, and the pit moulding is efficient and not subject to the effects of season.
The second step: pouring and heat treatment
The qualified raw and auxiliary materials shall be put into the arc furnace according to the proportion, and the sampling of hot metal shall be carried out to perform the spectral analysis. After qualification, the pouring shall be carried out according to the principle of "low temperature and quick casting", and the pouring time and temperature shall be recorded.
The third step: polishing and flaw detection
Finally, cut the pouring riser and burr etc. CHAENG has professional mechanical polishing teams and large-scale blasting apparatus, which can effectively improve the appearance quality of support roller, to meet customer’s requirements on surface finish. Moreover CHAENG take use of advanced detection equipment for non-destructive testing to ensure the internal quality of supporting roller, strictly stop any defective goods from leaving the factory.
Order online
Fill out your message and submit it . Options with * must be filled in.
Prev:Safety problems and solutions in the practice of slag pot for ferroalloy smelting
Next:Welcome the new year 2018, CHAENG steel castings want to tell you
PRODUCTS
CONTACT
- Tel: +8615290747879
- Whatsapp: +8615290747879
- E-mail: casting@chaeng.co
- Skype : GreatWall1958